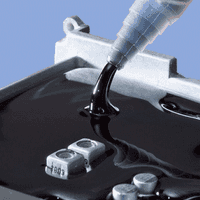
SD-PG20
SD-PG20 is a 2 part addition cure silicone. For easy application the product was designed with very low viscosity.
It cure at room temperature but it is possible to accelerate the speed by heat. This product has anti-toxic
property, low viscosity, good fluidity, low shrinkage after curing, and excellent flame-resistance, thermal conductivity and electrical insulation properties.
Features and Benefits
- Thermal conductivity: 2.0 W/m·K
- Two-component, room or elevated temperature curing system silicone
- Low viscosity and high flow
- Excellent low and high temperature mechanical and chemical stability
Typical Properties
PHYSICAL | TYPICAL RESULTS | TEST METHOD |
---|---|---|
Viscosity / Part A | 3,500 mPas | Brookfield 4# 10rpm |
Viscosity / Part B | 3,500 mPas | Brookfield 4# 10rpm |
Viscosity as Mixed | 3,500 mPas | Brookfield 4# 10rpm |
Density | 2.8 g/cc | GB/T 13354-1992 |
Mix Ratio | 1:1 | - |
Shelf Life @ 10-27°C | 12 months | - |
PROPERTY AS CURED | ||
Tensile Strength (MPa) | 1.0 | - |
Hardness, Shore 00 | 55 | ASTM D2240 |
ELECTRICAL AS CURED | ||
Dielectric Strength | 10kV/mm | ASTM D149 |
Volume Resistivity (Ω·cm) | ≥ 1x10¹¹ | ASTM D257 |
Flame Rating | V-0 | UL 94 |
THERMAL AS CURED | ||
Thermal Conductivity (W/m·K) | 2.0 | ASTM D5470 |
Pot life @ 25 °C | 60 mins. | - |
Cure @ 25 °C | 12 hrs. | - |
Cure @ 80°C | 30 mins. | - |
Working Temp. | -50-180°C | - |
Typical Applications
- Automotive electronics
- Power supplies
- Connectors
- Sensors
- Industrial controls
- Transformers
- High voltage resistor packs
Available Forms
- Supplied in 20KG barrel
Directions for Use
Oven atmosphere: nitrogen (recommended) or air;
The existence of some substances could inhibit or influence curing:
Organic tin and other metal compounds;
Silicone rubber containing tin catalyst; Sulfur, sulfur compounds, polysulfone compounds or other sulfur-containing compounds; Amine, polyurethane rubber or other ammonia containing substances; Phosphorus containing substances; Unsaturated hydrocarbon plasticizers; Flux residues, etc.
Clean the surface of pasted object to get rid of oil, water, dust, and other impurities;
Weight Part A and Part B accurately;
Blend: Mix the Part A and Part B evenly, using vacuum degassing if necessary.
(Some sediment maybe exist in the bottom of Part A or Part B. Please stir evenly before mixing.)
Pouring: Mixture should be used up within the working time, otherwise its viscosity will increase leading to it not suitable for pouring.
Contact us to have your questions answered, to obtain free samples, arrange prototypes/small batch runs, and discuss customized solutions for your projects.